Flexo Printing, some of the time referred to as “surface printing,”. It is a technique that we usually use for printing on packaging and other uneven surfaces. In “Flexo,” the plates we use in the printing procedure are regularly made of rubber or flexible plastic. This permits the inked surface to adjust to numerous sorts of substrates.
These inks, not at all like those used in lithography, for the most part, have low consistency. It is similar to the case with the inks used in gravure. This quality makes the two procedures quick-drying, which thus brings about generally high speeds of creation for the two methods.
WHAT IS THE FLEXO PRINTING PROCESS?
This printing is famous for accomplishing top-notch printing pictures at high generation speeds. It is the settling on it a well-known decision in the food packaging, materials, and label printing enterprises. Used for particularly for longer print runs.
The Flexo Printing (Flexo) printing shares much for all intents and purposes with different types of rotational printing, however with added flexibility because of the capacity to hybridize Flexo presses with new computerized advancements to help profitability and decrease costs.
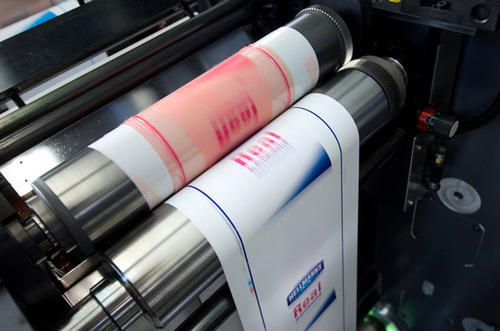
The Flexo procedure has been working over many, numerous years and has remains adamantly well-known over a wide range of printing divisions. It is adaptable, utilizes speedy drying ink, and is appropriate for a wide scope of substrate materials. This article will assist you in seeing how we do the printing procedure.
PRINTING PLATES in Flexo Printing
So as to comprehend the flexo print process, we first need to see how the printing plates are made.
Starting of Procedure
The necessary picture is first uncovered onto a film negative, using a laser imagesetter, or legitimately onto the plate (with a pre-laminated negative mask), using Computer to Plate (CTP) innovation. Then we present the plate and film to UV light so as to fix the picture into the polymer material. Just the straightforward zones of the negative film/covered mask will permit the UV light to go through, empowering the UV beams to change the atomic holding in the photopolymer material.
Middle Stage of Procedure
After adequate presentation time, the plate is then prepared for the washout process. The washout arrangement can be water or dissolvable, contingent upon the sort of plate material. The unexposed regions of the polymer are then washed away from the plate base, through a washout brush. We disintegrate the waste polymer into the washout arrangement, which we afterward handle for reusing/solvent recovery.
Last Segment of the procedure
Following the washout process, the plate is then set in a hot air dryer, where overabundance water/dissolvable dissipates, leaving a dry plate. A postfix is then required, using both UVA and UVC lights, after which the completed plate is prepared for use.
PRINTING PROCESS in Flexo Printing
The printing plates are mounted onto round and hollow plate rollers, which are then stacked into the flexo press, with each necessary shading situated in progressive print stations. As every roller turns, the plate gathers ink from the inking roller (anilox roll) and afterward moves the inked picture onto the substrate. The wet ink at that point goes through a dryer, before the following shading is printed.

The substrate is fed into the press in move structure, from the loosen up station. The pressure of the material is deliberately checked and controlled to guarantee that all hues are printed in register. Any in-line adornment or changing over is at that point completed, before rewinding or sheeting.
Adaptable INKS in Flexo Printing
Flexo inks should be quick-drying and are by and large water-based, solvent based, or UV relieved. The sort of work, length of run and regularly substrate type would decide the ideal ink type. The flexo procedure empowers the utilization of a range diverse ink viscosities, permitting expert inks to be used for applications, for example, security print, light-quick outside labeling, fluorescent and metallic impacts, and so forth.
There is additionally the accessibility of food-grade ink for food bundles and environment-friendly inks.
ADVANCES IN FLEXO PRINTING
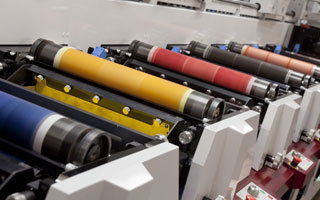
Because of advances in innovation, Flexo printing process has developed into an exceptionally effective print process, delivering the highest caliber of printing. Flexo is adaptable and steady, giving quality print and solid repeatability. This sort of printing can be seen wherever from the grocery store racks, to shopping bags, tickets, labels and numerous different applications.
To get the best out of Flexo printing, you have to comprehend the procedure efficiently.
FLEXO PRINTING MACHINERY AND EQUIPMENT
As one of the quickest developing customary printing forms in packaging, films and layered compartments, Flexo printing is adaptable, solid and produces premium quality outcomes.
At first simple in printing quality, the printing style’s development since the 1990s in print machines, plates and inks have accounts for predominant outcomes and we currently use broadly in process shading printing on a wide choice of materials and we have discover all the more normally in limit web printing.
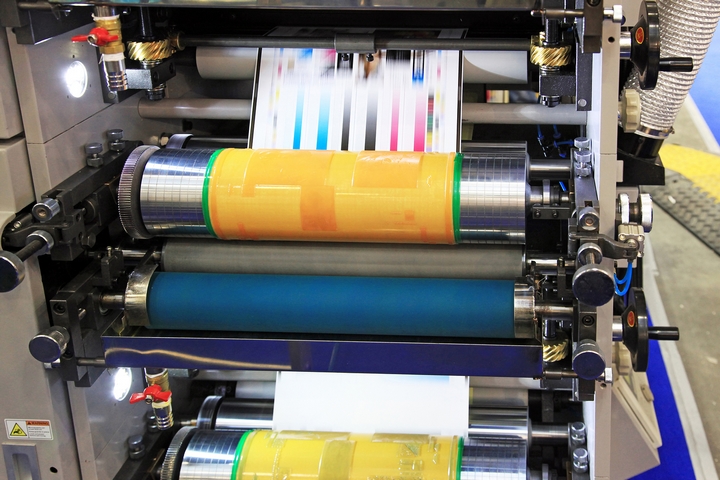
Much like a letterpress, our Flexo printing machines utilize adaptable printing plates made of rubber or plastic. These are inked with a picture which is turned onto a chamber and afterward moved onto the picked material. You will find that our scope of machines all utilization quick drying inks and work at high speeds which would all be able to be altered. This implies you can cook your picked bit of Focus Label printing hardware to suit your ideal yield and prerequisites.
At Focus Label we plan and production a wide choice of paper and packaging gear appropriate for different Flexo printing results which you will discover underneath. Regardless of whether you require increasingly bespoke printing alternatives for bigger components of material or high volumes of generation, we can prompt you on the correct choice to suit you.
Different machines are accessible for various Flexo Printing applications, anyway should you have more master prerequisites or be not able to locate a specific printer that suits your needs then we can guide you further.
With our broad experience and information on the printing business we can likewise help you as far as the correct preparing and backing to suit your motivations or workforce.
5 Different Flexo Printing Advantages and Disadvantages
Flexo printing is a printing style that utilizations ceaselessly fed material to create prints of high caliber at high speeds. This style of printing is commonly used for enormous quantities of prints, so it is perfect for a wide range of item labels.
Flexo printing is reasonable for all intents and purposes any substrate or material that can be web-fed. Likewise, the wide range of inks that can be used in Flexo printing take into account it to reliably create unimaginably top notch prints, regardless of the material.
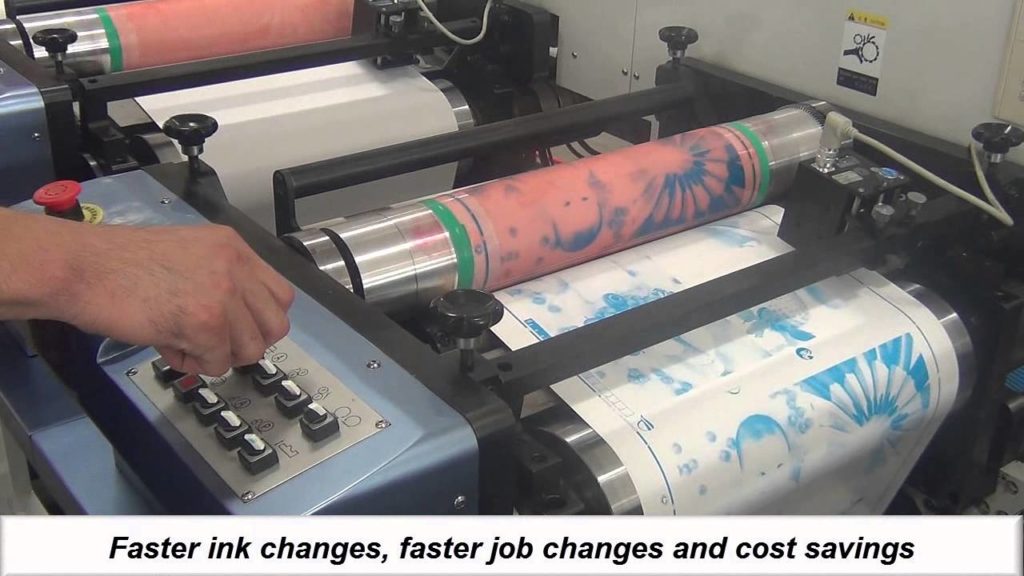
Here are the five diverse Flexo Printing pros and cons:
1. Advantage: Highly Automated Flexo Printing
The Flexo printing process is exceptionally mechanized once it has started. The material feeds from an enormous move that goes through to each plate that is being used, individually. The plates roll the ink onto the material, and once the name has been totally printed, the chopping kick of the bucket isolates each structure down into its appropriate, uniform size.
This whole procedure is finished consequently in Flexo printing; though in different kinds of printing a portion of these means requires difficult work.
2. Advantage: Cost-effective Flexo Printing
Flexo printing is prudent in value, contrasted with different kinds of printing. This is somewhat because of the low work costs required to finish an occupation, the quick turnaround time, and the minimal effort of the vast majority of the materials, similar to the ink which is a lot less expensive for Flexo printing than for other printing techniques. The principle costs engaged with Flexo printing are the expense of the plates: each shade of a name requires its own one of a kind plate, and, obviously, there is an expense related to everyone.
Be that as it may, because of the low expenses related with the remainder of the Flexo printing process, we look it as an efficient printing alternative, particularly for enormous printing orders.
3. Advantage: Fast Flexo Printing
Since the material we use for Flexo printing is web-bolster, this permits the printer to take advantage of the space it has, fitting the plan whatever number occasions both vertically and on a level plane as could be allowed. Thusly, Flexo Printing printers can turn out a high volume of substance every hour.
The quickest present day Flexo Printing printers can turn out up to 750 meters of printing every moment. That is around 45 kilometers 60 minutes! There’s no uncertainty that where speed is concerned, all other printing techniques meet their match with Flexo Printing.
4. Disadvantage: Not perfect for littler employments in Flexo Printing
Flexo Printing offers numerous advantages, yet they are equipped more towards enormous printing occupations. There is no point setting aside the effort to configuration plates and do an entire arrangement for a little request – this would almost certainly remove a portion of the advantages that accompany Flexo Printing, as the structure and creation procedure of the plates can be tedious and exorbitant. Obviously, when the printing request is critical, these downsides are made up with the rapid and low working costs engaged with the procedure.
Notwithstanding, organizations ought to dissect and analyze, in light of the fact that it might in any case be valuable to decide on Flexo Printing printing on a littler request, contingent upon the quantity of plates that will be required, and if this request would be rehashed later on.
5. Downside: Setup can be tedious in Flexo Printing
As the whole procedure is mechanized, the arrangement time is longer. Somebody must introduce the material, set up the hues to the right plates, wrap the plate chambers with the right plates, and introduce the best possible cutting pass on. This procedure takes time, and once more, with bigger requests that arrangement time is made up with the amazingly fast of the printing. Nonetheless, if the request is littler it may not be justified, despite all the trouble to invest such a great amount of energy in arrangement just for the request to be finished in almost no time.
6 Products You Don’t Know we Create With Flexo Printing
One reason behind its prevalence is its adaptability.
Flexography Capabilities
Its flexibility gets from the capacity for flexo to print on an assortment of substrates – from film to paper, to thwart, to folded, and then some.
Remembering that, there are a ton of items that you see pretty much each and every day, and likely weren’t even mindful were print by using flexo printing.
Here’s a gander at the absolute generally prominent:
1. Specialty BEER AND WINE LABELS by Flexo Printing
The specialty lager and wine labels are blasting at the present time, and quite a bit of this is because of how the different distilleries showcase their brands.
Psychologist sleeves are normally the name of decision with regards to brew jugs and a few jars, and flexo can create structures with a significant level of detail.
Since flexo has printing abilities on such a wide assortment of substrates, there truly isn’t a specialty brew or wine name that flexo can’t print.
In the wake of printing, wine labels would then be able to be emblazoned – which sets extravagance make wine labels separated.
2. Regular CANDY WRAPPERS AND BAGS by Flexo Printing
Flexo is likewise a perfect printing innovation for making enormous amounts of occasional things, for example, treat wrappers.
At the point when shopper item organizations (CPCs) are hoping to switch up their packaging to give certain items an exceptional occasion pizazz, flexo is regularly the favored innovation to complete it.
By essentially making new picture transporters, or modifying the shading plan on existing picture bearers, CPCs can include that regular touch their clients are searching for with regards to specific times of the year.
3. PAPER TOWELS by Flexo Printing
Gone are the times of apathetic paper towel printing – and this is to a great extent on account of flexo. Today, many paper towel brands have progressed to where this regular family unit great seems as though it was redone by a prestigious planner.
Basically, flexo printing has helped transform paper towel into a kitchen style explanation, as customers can pick dependent on brand, however on the structure they like.
Who might have ever imagined that something as apparently basic as paper towels could ever be equipped for looking so cool?
4. METAL PANELS FOR SIDING AND ROOFING by Flexo Printing
One astonishing application for flexography is to deliver metal siding and material for home and business building.
The boards can be structured unpredictably with flexo, in any event, emulating a wood grain – or black-top or cedar shingles as appeared in the photograph above. For purchasers, this metal item can offer the strength required to continue a long time to come while highlighting an interesting structure.
5. PIZZA BOXES by Flexo Printing
Ever considered what innovation is behind the printing on your pizza box? Indeed, next time you bring in a conveyance, realize that it was most likely flexo liable for printing the container that you’re eating out of.
Flexo, in contrast to some other printing techniques, can print straightforwardly onto layered when essential.
Cardboard pizza boxes are absolutely a fit, and numerous pizza shops are exploiting the printing system to print long runs of their crates – and in a cool, inventive way that can be both enlightening and ornamental for clients.
What’s more is that it’s a protected innovation that can be imprinted on holders – and for this situation, boxes – putting away food.
6. Embellished PRODUCTS by Flexo Printing
Embellishing is something that regularly recognizes extravagance brands and products from others. It might likewise be used on wine bottles, on scent containers and that’s just the beginning, and the enormous advantage of decorating is that it can transform a standard name into a 3D perfect work of art.
Embellished labels bid to two detects – sight and contact – and CPCs regularly utilize this procedure on items that they truly need to grab the eye of the customer.
So whenever you get a jug of aroma, or top rack alcohol, with a decorated label, realize that it was likely made using flexo.
FLEXO PRINTING VS. Offset PRINTING
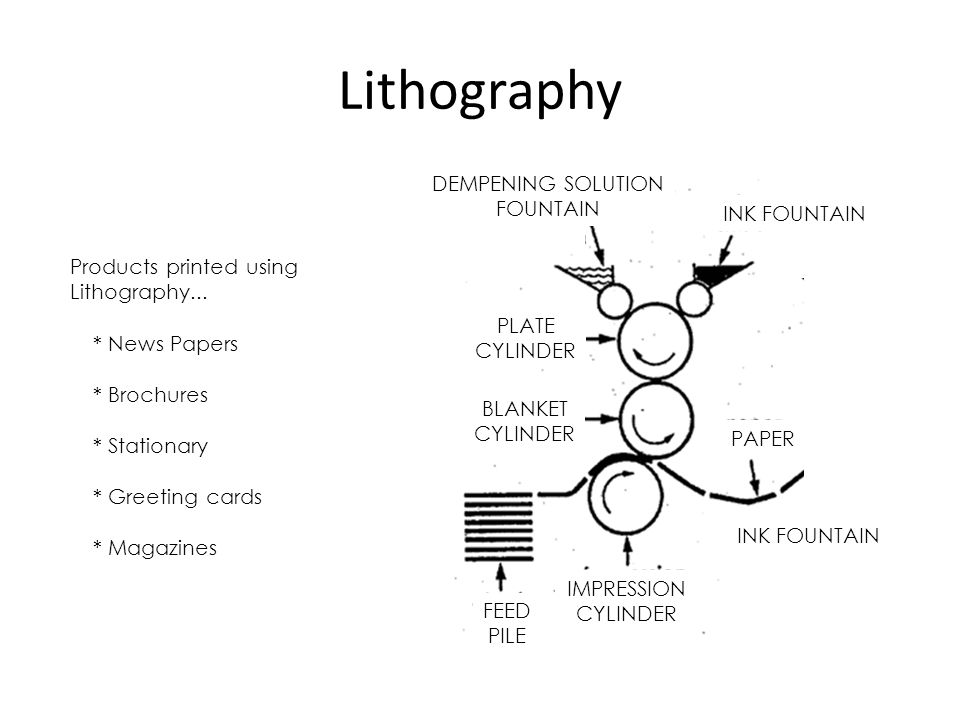
Albeit the two strategies utilize wet ink and printing plates, these two printing forms are very unique. In fact, offset printing can allude to any printing system that uses a printing plate to move a picture to the middle of the road bearer and afterward onto the printed substrate. While flexo moves ink from the plate straightforwardly to the substrate.
Flexo and counter offset are both well known, however they play out their errands in an unexpected way. It is essential to comprehend what jobs they perform and have an away from of the two kinds of printing process. The kind of press to utilize relies upon the last item and quality required, just as volumes and substrates.
Distinction 1: PLATES
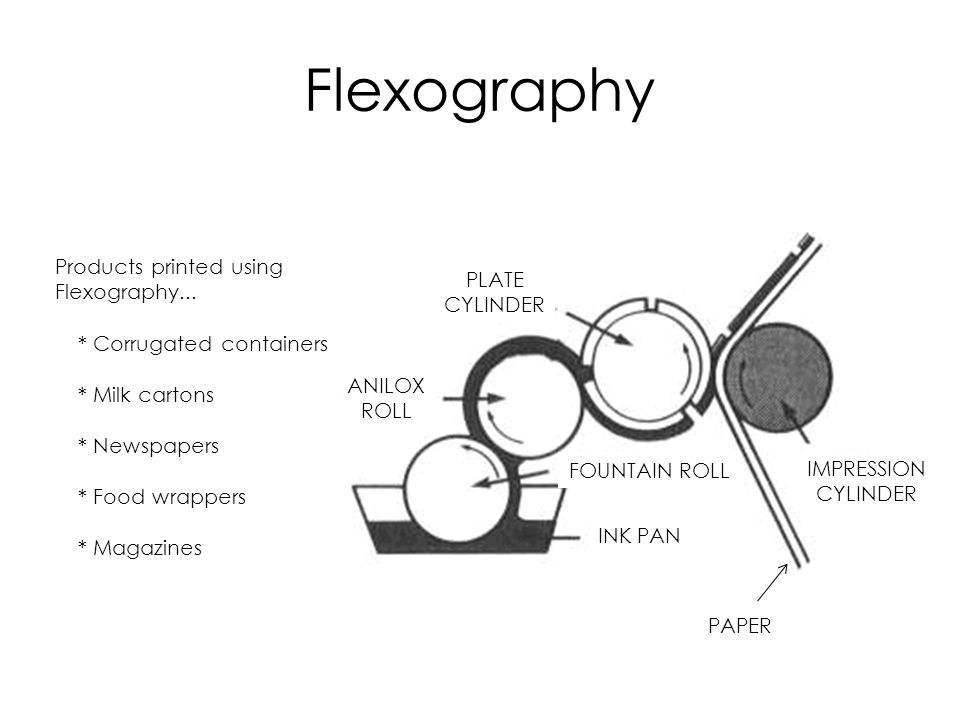
As the name proposes, flexo printing uses adaptable plates for a rotating printing process. We produce the plates using a photopolymer compound and are adaptable enough so that we fold it over a printing chamber. The help picture on the plate we fix by means of a laser picture setter and the polymer in the ‘non-print’ regions which we wash away in a handling unit, where it disintegrates into a dissolvable or water arrangement. We move ink from the ink well through a turning ‘anilox’ roller onto the flexo plate. A different printing station and flexo plate is required for each shading to be printed. The picture is then printed straightforwardly onto the substrate. The printing plates are very solid and whenever put away effectively, can be re-used a few times, before they in the end should be supplanted.
For offset printing, again as the name proposes, ink is moved (counter offsetd) by means of a progression of rollers onto the printing plate. This can be either a level bed or revolving process – relying upon the sort of offset press. The plate is generally made of aluminum. The total wet picture (either single shading or multicolor) is then moved onto a ‘cover’ and thusly onto the substrate, before drying.
Distinction 2: INK
Counter offset printing, for the most part, comprises of four ‘process’ hues; cyan, fuchsia, yellow and key (which is dark). Each shading has a committed printing station. We produce any spot hues using a mix of the procedure hues. Ink can be water-based or UV treatable.
In spite of the fact that procedure hues are likewise used in the flexo procedure, extra print stations will, in general, be used for spot hues. Spot hues can be provided pre-blended or can be blended in-house, as required. Flexo inks can likewise be water-based or UV treatable. Dissolvable based inks can likewise be used. UV inks empower higher running velocities and can be left in the press by the day’s end, without the need to discharge and clean each print station. Water-based inks should be expelled from the press, when it isn’t being used – to keep ink from drying on the rollers and in the ink plate.
Distinction 3: TYPES OF MATERIALS TO PRINT ON
Counter offset printing machines can print on materials, for example, paper, metal, cardboard, cellophane, and vinyl. The printing surface must be level and smooth. It is great for printing papers, books, magazines, stationery, notices, leaflets, etc. For the most part, to print onto the two sides of the substrate will require a subsequent pass. Likewise, amazing, cutting, collapsing, wrinkling, overlaying, and so forth is done as an auxiliary, disconnected procedure.
Flexo Printing is used on both permeable and non-retentive materials, for instance, cellophane, foil, cardboard, texture, plastic, metal and so on. It is for the most part used for packaging; envelopes, retail sacks, backdrop, paper, papers, sweet wrappers, labelstock, etc. The primary distinction with the two procedures is that counteroffsetd printing is just done on level surface while Flexo printing can be used on practically any substrate with an adaptable surface. Flexo printing can accomplish rapid creation and numerous presses have various changing over alternatives coordinated into the press, empowering a solitary pass activity.
Flexo Printing versus Gravure Printing: Key Differences
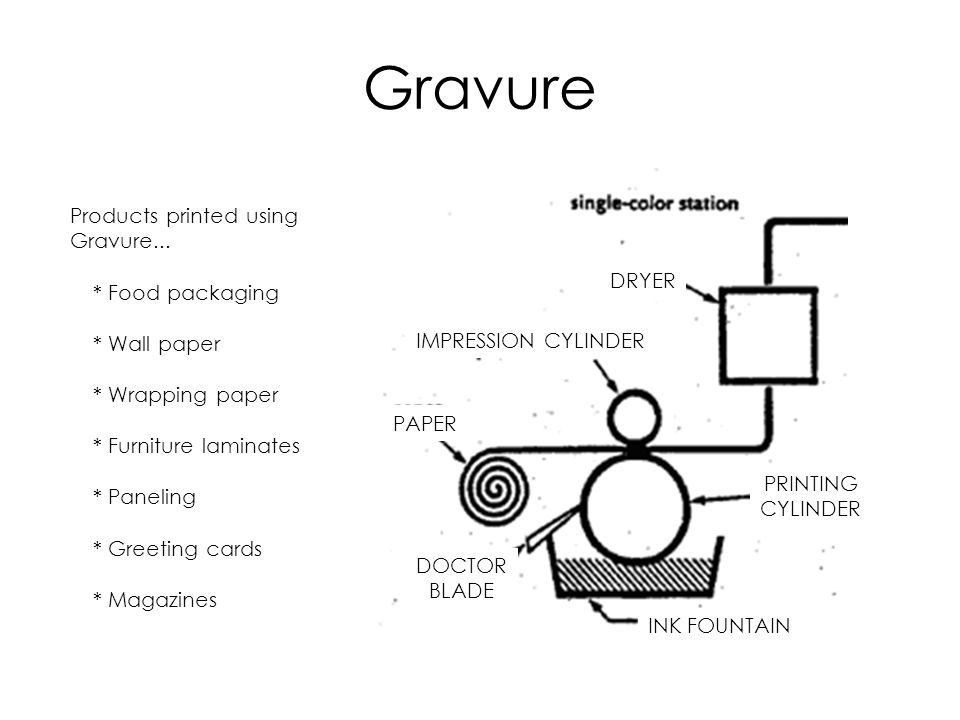
Since we’ve gone over the likenesses among flexo and gravure, and clarified the fundamental procedure of every, it’s an ideal opportunity to investigate a portion of the key contrasts:
COST AND LEAD TIME:
Gravure picture bearers are normally significantly more costly than flexo picture transporters, making the quantity of prints required to equal the initial investment a lot higher. Gravure, in any case, has a more drawn out press run time as the chambers don’t require as successive changing as flexo.
Gravure lead time is generally 3-4 times that of flexo in the time it takes to fabricate the picture transporter.
SUBSTRATES:
One of the restrictions of gravure printing is that it is commonly more qualified for permeable substrates. This is one reason that gravure is most appropriate for high detail printing on applications, for example, magazine covers.
That isn’t the situation with flexo printing, which can print on both permeable and non-permeable substrates, making the innovation perfect for everything from film to paperboard.
INKS:
Another key differentiator is the scope of inks flexo can print with. Gravure is increasingly constraining in the inks that it works with, frequently settling on flexo the better decision due to the simplicity of printing with a more extensive assortment of inks.
Gravure requires significantly more ink per print, which can drive up the expense of printing.
Environment-Friendly:

Because of the way that gravure is generally connected with dissolvable based inks, despite the fact that water-based ink abilities have been developing, we call flexo the “greener” choices.
Flexo by and large has more choices for VOC contemplations, and the press tasks are related with all the more ecologically cordial practices.
QUALITY:
Gravure was once viewed as best for fine detail and tonal work, yet flexo innovation is further empowering prints with higher goals and detail as it develops – empowering it to move into print employments that were recently related only with Gravure.
Coming on THE RIGHT CHOICE in Flexo Printing
Every one of the three Flexo Printing, Gravure Printing and counter offset Printing have their points of interest. Flexo Printing is great for fast creation and by and large quality. It is incredible from numerous points of view and is commonly fitting for most huge scale printing assignments. In the label printing segment, most organizations favor Flexo printing as a result of its versatility and economy of scale. When searching for a printing arrangement, search for one in light of things to come, and put resources into the printing innovation of things to come. One current pattern for flexo we join with advanced printing innovation to create incredible half breed arrangements that outflank most customary counter offset presses.
Flexo Printing beats offset printing as a rule as a result of its adaptability and profitability benefits. A Flexo Printing press is a sound, long haul venture and is sufficiently versatile to oblige and coordinate a wide scope of in-line forms, including new advanced innovation.
The power is to set the agenda. What we print and what we don’t print matter a lot.
So what procedure is directly for you? It to a great extent relies upon the activity, substrate, and an assortment of different elements of the activity you’re printing.
We are an exporter of printing and publishing materials. Write a blog on printing tech, tricks and strategy is my passion. We are suited at 249/2, opposite Vasant Vihar Bus Depot, Munirka New Delhi -110067, near Indira Gandhi International Airport, India. We provide our services in Pan India and all major countries in the World.
(M) 9211253015
Email:sureshshivanienterprises@gmail.com
Website: https://www.shivanienterprises.com
You can also have a look at
https://www.linkedin.com/in/suresh-kumar-b2348555/
https://in.pinterest.com/sureshshivanien/
https://www.instagram.com/sureshshivanienterprises/
https://www.facebook.com/shivanienterprises/